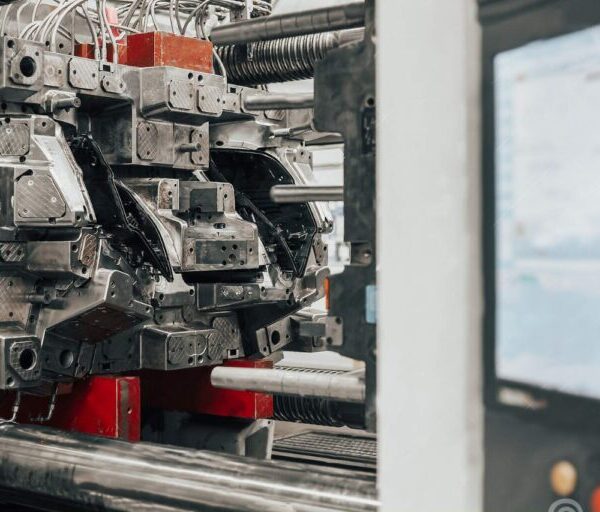
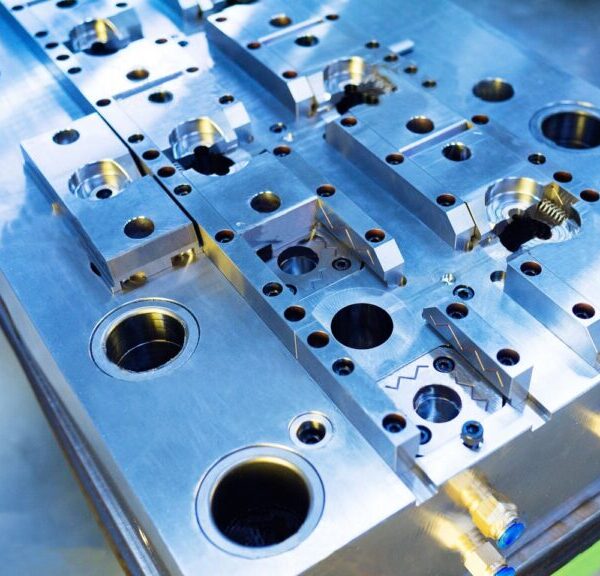
Moulding
At Premier, we specialise in the production of demanding customer products which may require any combination of close tolerances, aesthetic external finishes and engineering polymers coloured to a match specification.
Our current machine line-up of more than 250+ machines ranges from 50-1200 tone clamp force. All of our machines are microprocessor controlled and capable of exacting tolerances with a high level of repeatability. Our machines are also monitored through our process monitoring system within a fully closed process-controlled loop.
120+
MOULDS IN A YEAR
60
DAYS AVERAGE LEAD TIME
40
PROJECT MANAGEMENT TEAM
co-molded plastics
We operate twin shot machines with rotating platens and vertical barrels producing co-moulded products.
High quality tooling, state of the art moulding machines and tight process controls are used to produce precision parts to close tolerances.
Lenses are produced from high quality injection mould tools with a high gloss surface finish. Manufactured in a controlled environment to prevent colour contamination.
Fine plastic thread forms are produced from precision injection mould tools utilising rotating core technology.
Ultrasonic & Heat Stake Welding gives the design freedom to produce a product with complex geometry. Finished assemblies can be in-process pressure tested to prove weld integrity.
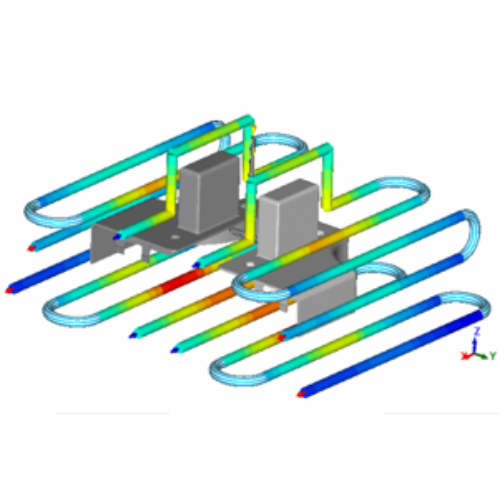
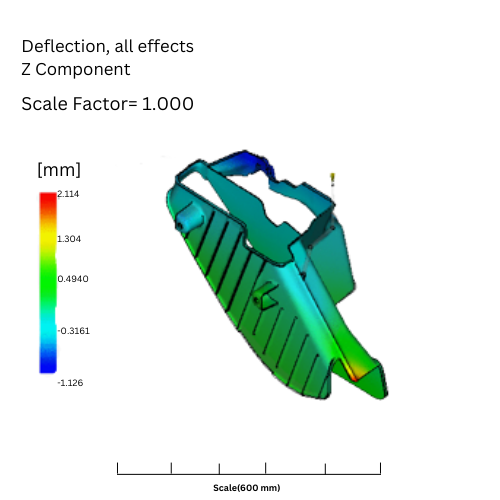
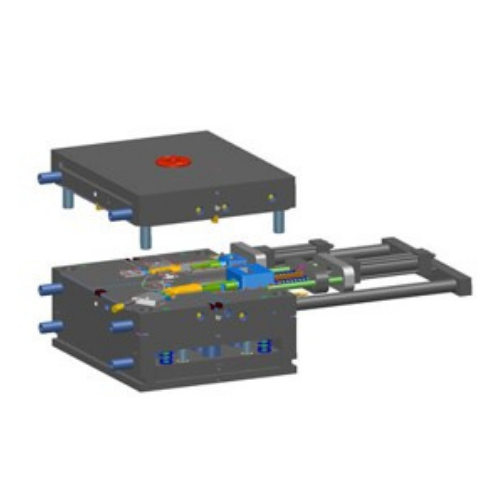
Tool Manufacturing
We have the capability to handle multiple suites of tools and in-house tooling of up to 7 tons, along with an array of high speed machining centres, CNC spark erosion & Die Spotting machine capabilities, means we can guarantee quicker turnaround and reduced product costs. All our machining centres use laser scanners and CMM machines to ensure precision, while our experienced toolmakers ensure the customer’s requirements are fulfilled to the very highest standards.
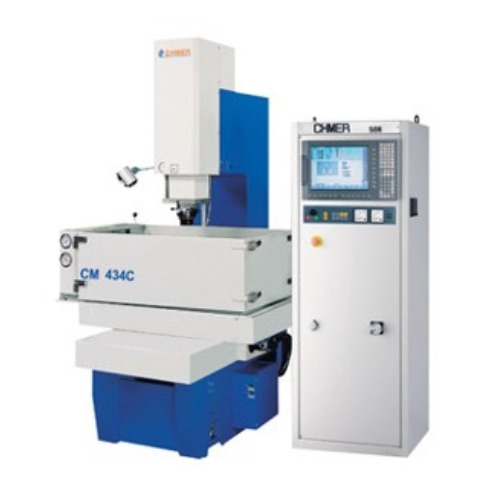
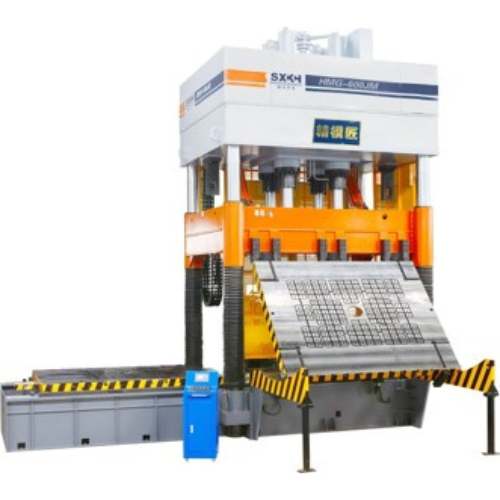
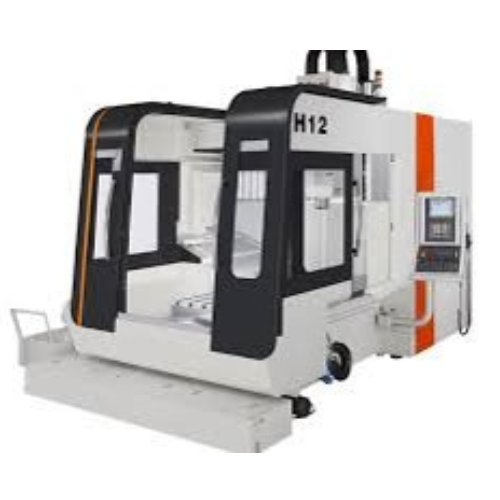